開発経緯は下ピン無しのストリッピングシステム(ストリップレンジャー)を構築中に立会いで①完璧に取れてた打抜機で1年後位に取れなくなった事がオンメン位置関係がズレてた事や、②取れない穴カスが急に出てきた事を見ると数枚置きに取れていない状況で明らかにグリッパーバーが7本で有れば7枚置きに落ちていない現象がグリッパーバーの問題と認識出来た事からダメなグリッパーバーの特定をしないといけなく成り丁度ふたつの事例が重なった事でストリッピング位置精査システム開発しなければいけなくなった。
①の事例は下ピン無しのストリッピングでオス型を12mm板で作製して通常のフレームをオス型だけを操作盤側からスライド式で簡単に固定できるオス型フレームに改造して今では当たり前に成ってるシステムを昔に構築した事からで有った。それで落丁出来てたシステムが段々と取れにくく成り調査に入った。調査結果はストリッピングオス型枠は動かす事が無く成ったのだがオス型枠を操作盤側反対側に有る位置固定ボルトが緩んでいた事でオス型左右位置がズレていた事が原因だった。この事から現在は此の方法を奨励しなく成りオス型は正確な位置決めされたメス型に合わす方法で奨励して推し進めている。
②は、細い溝穴がクワエ反対側で数か所取れない事案が有りたまたま、K判サイズの抜き商品でクワエ反対側が落ち難い事案が有り、グリッパーバーの僅かな歪みがクワエ側から遠いと落ち難いと云う知識が有り、どのグリッパーか特定しないといけない事案だった事で解決出来た。
日本での下ピン無し技術取込みが出来ない理由が打抜機のメンテナンスの悪さが原因と成っている。又、右図の様に各ステーションでのストッパーがストリッピングステーションには付いていない打抜機はチェーンピッチのみでの場合も有る。いずれにしても打抜機精度が現在の打抜機には全般的にメンテナンスの悪さから下ピン無を取りこめる仕様には程遠いのが現状で有る。
又、打抜機自体が高スピード化に伴いグリッパーバー厚みが薄く成るにつれ、簡単な抜型部品との衝突で微妙な歪みが発生している打抜機も多々あります。この事を定期的に精査して打抜機精度メンテナンスが必ず必要に成るのが下ピン無のストリッピングだ。
※概要・・・打抜ステーションでテスト用紙に抜型で4隅に+に刃を入れます。次にストリッピングステーションでオス型とメス型で各4隅の+刃の痕に対角で内側と外側にオス型とメス型に配置した突針で痕を付けます。このテスト用紙はグリッパーバーの本数分を出来る限り通常打抜速度で通紙する。グリッパーバーに一本にテープを貼り動画を取れば何枚目がテープ付きグリッパーバーが咥えたかを判別する事で正常で無いグリッパーバーの特定も出来ます。尚、テスト用紙は薄口と厚口と段ボールの各縦目横目で通紙する事が望ましい。(垂れ下がりで位置ズレが有る場合が多い)
・位置精査抜型
抜型は任意の位置で4隅に+の刃が入っています。+中心部は隙間が有ります。
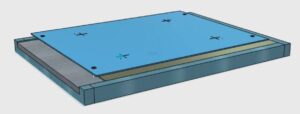
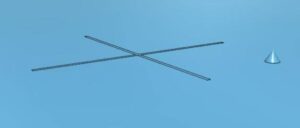
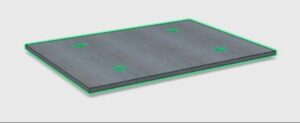
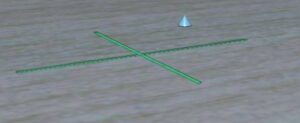
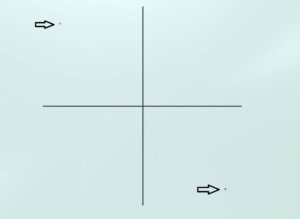
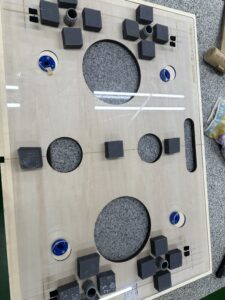